1. Номенклатура
Номенклатура технических материалов служит для описания совокупности материалов, используемых при изготовлении машин и других технических изделий. Знание номенклатуры герметизирующих материалов необходимо для обоснованного выбора конструкции уплотнения, технологии и режимов эксплуатации материала в составе уплотнения. В основе номенклатуры лежит система соподчиненных понятий, устанавливающая связи между группами материалов. Принимая во внимание многообразие герметизирующих материалов, выделим по признаку агрегатного состояния твердые и жидкие материалы, а также газы и плазму.
Газы как герметизирующие материалы применяют в эжекторных уплотнениях, отводя с помощью газового потока герметизируемые среды от зазоров в соединениях. Таким образом, используют водяной пар, воздух, азот, углекислый газ, аргон и др. Определяющими параметрами являются их плотность, вязкость, теплофизические характеристики и химическое сродство с герметизирующими средами.
В некоторых случаях функции герметизирующего материала выполняет пар герметизируемой жидкости. Например, в торцовых уплотнениях, называемых уплотнениями паровой фазы, нагревают герметичное подвижное соединение выше температуры кипения герметизирующей среды. Если последней являются легкокипящие жидкости, они переходят в газовую фазу прежде, чем попадают в зазоры соединения. Таким образом, предотвращается кипение жидкостей в зазорах, которое дестабилизирует работу герметичного соединения и приводит к повреждению поверхности трения. Этот прием особенно эффективен при использовании паров воды и ее растворов (гликолевых, глицериновых и др.), легких углеводородов и масел. Его применяют также в уплотнениях для криогенных жидкостей, чтобы обеспечить работу пары трения в режиме газовой смазки. В насосах, перекачивающих криогенные жидкости (азот, гелий, аргон и др.), пары последних нагнетают в зону трения торцовых уплотнений для реализации газостатических сил и уменьшения износа.
Наиболее характерно применение газов в качестве, герметизирующих материалов для разделения герметизируемой и окружающей уплотнение жидкостей. Газовые затворы, в которые напускают гелий, неон, аргон, криптон и т.п., предотвращают растекание, смешивание, химические реакции, фазовые переходы и другие последствия контактирования жидких сред в уплотнениях.
Плазма – частично или полностью ионизированный газ, в котором плотности положительных и отрицательных зарядов практически одинаковы. Плазму используют в качестве герметизирующего материала в эжекторных уплотнениях, предохраняя соединения деталей реактивных и турбореактивных двигателей, форсунок, горелок и других устройств от воздействия основной плазменной струи. Механизм герметизации газового потока, заключенного в трубчатую оболочку из плазмы (рис. 4), можно представить как результат взаимодействия плазмы и внешнего магнитного поля В. Возникающие при этом объемные электродинамические силы уравновешивают давление газового потока.
Жидкие герметизирующие материалы широко используют в технике. Наиболее типичными из них являются магнитные жидкости – коллоидные суспензии частиц магнитного материала. Первая магнитная жидкость была получена в 1964 году и представляла собой коллоидный раствор магнетита в керосине. Частицы магнетит с размером около 10-2 мкм для предотвращения слипания содержат покрытия из ПАВ. Магнитные жидкости обладают необычным сочетанием свойств – намагниченностью и текучестью. В магнитном поле они приобретают магнитный момент, который лишь на порядок меньше магнитного момента твердых магнетиков. В настоящее время созданы магнитные жидкости на основе воды, толуола, эфиров, фторуглеводородов, минеральных и синтетических масел, содержащих коллоидные дисперсии практически всех известных ферромагнетиков.
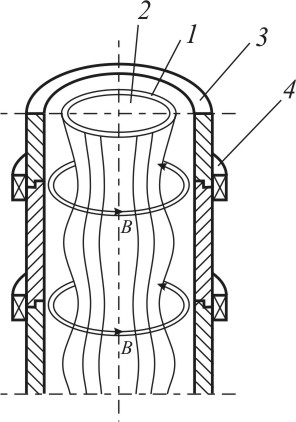
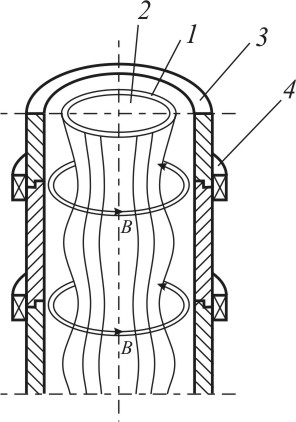
Рис. 4. Регулирование конфигурации газового потока с помощью плазмы: 1 –
канал плазменного разряда; 2 – газ; 3 – трубопровод; 4 – магнитные катушки
канал плазменного разряда; 2 – газ; 3 – трубопровод; 4 – магнитные катушки
В номенклатуре герметизирующих материалов широко представлены уплотнительные смазки – мазеобразные составы, получаемые введением в жидкие масла твердых загустителей. Последние образуют структурный каркас, в ячейках которого удерживается масло. При небольших нагрузках смазки подобно твердому телу не растекаются, а при больших – текут, как вязкие жидкости. После снятия нагрузки течение прекращается, так как каркас обладает свойством восстанавливаться. Как герметизирующие материалы смазки более эффективны, чем масла, особенно при значительных перепадах давления. Они хорошо удерживаются в узлах трения, предотвращая задиры и схватывание при υ < 0,1 м/с, а также защищая металлические детали от коррозии. Наиболее важные показатели свойств смазок связаны с их поведением под нагрузкой: предел прочности на сдвиг характеризует способность удерживаться в подвижном соединении, вязкость – течение в жидком состоянии, механическая стабильность – восстановление структуры после снятия нагрузки.
Уплотнительные смазки подразделяют на группы, предназначенные для применения в запорной арматуре, резьбовых соединениях и вакуумных системах. Смазки для запорной арматуры нефтяных скважин, нефте- и газопроводов, где рабочее давление достигает 100 МПа, получают на основе касторового масла, глицерина, гликолей, олефинов и других синтетических жидкостей, загущенных мылами, силикагелем, бентонитами, органическими полимерами. Обязательным компонентом смазок являются наполнители: графит, тальк, слюда, асбест, металлы и др. Смазки для резьбовых соединений труб готовят на основе термостойких масел, загущенных металлосодержащими соединениями и содержащих антифрикционные наполнители. Для изготовления вакуумных смазок применяют узкие фракции высокоочищенных нефтяных и синтетических масел, которые загущают углеводородами, мылами и неорганическими соединениями. С целью повышения адгезии в них вводят полимерные добавки. В последние десятилетия номенклатура пластичных смазок значительно расширена благодаря использованию новых присадок, загустителей и наполнителей. Разработаны смазки, обладающие электропроводностью, магнитными свойствами, стабильностью при высоких давлениях.
Герметики – пастообразные или вязкотекучие массы на основе полимеров и олигомеров, отверждающиеся в зазорах соединений с образованием прослоек, которые препятствуют утечке сред. По деформационно-прочностным характеристикам они занимают в ряду машиностроительных материалов положение, между клеями и резинами. Номенклатуру герметиков составляют термореактивные и термопластичные материалы. Термореактивные герметики вследствие образования химических связей из исходного текучего состояния необратимо переходят в эксплуатационное эластическое состояние. К ним относят вулканизующиеся материалы, сшивающиеся под действием отвердителей, герметики полимеризующиеся при отсутствии кислорода в зазорах соединений. Термопластичные герметики подразделяют на невысыхающие и высыхающие. Невысыхающие герметики – обратимо переходят из исходного вязкотекучего в эксплуатационное пластическое или высокоэластическое состояние. Для их получения используют высоко- и низкомолекулярные каучуки (полиизобутиленовый, бутилкаучук, этиленпропиленовый и др.), полностью насыщенные или с малым количеством двойных связей в молекулах. Путем повторного растворения их можно возвратить в вязкотекучее состояние. Высыхающие герметики готовят на основе высокомолекулярных вулканизирующихся синтетических каучуков (бутадиен-стирольных, бутадиен-нитрильных, хлоропреновых и др.), а также термоэластопластов в сочетании со смолами. Основными характеристиками герметиков являются газопроницаемость при рабочих температурах, адгезия к конструкционным материалам, вязкость в исходном состоянии и др. Специфический показатель герметиков – жизнеспособность, т.е. период времени, в течение которого сохраняются их исходные технологические свойства.
Расплавы металлов как герметизирующий материал сочетают жидкотекучесть и большую удельную массу. Как правило, в уплотнениях используют цветные металлы, испарения которых токсичны. Поэтому области их применения ограничены главным образом замкнутыми системами, вакуумной и космической техникой.
Расплавы полимеров и вязкоупругие полимерные жидкости – сравнительно новый вид герметизирующих материалов. Расплав полиизобутилена с молекулярной массой 103 – 105 используют в тихоходных динамических уплотнениях, эксплуатируемых при воздействии вибраций.
Низкомолекулярные жидкости в качестве герметизирующего материала выполняют преимущественно функции разделительных сред. Их применяют в следующих основных случаях: давление перед уплотнением ниже атмосферного; герметизируемой средой являются агрессивные, взрывчатые, токсичные и другие экологически опасные вещества; уплотнение работает в гидроабразивной среде с большим содержанием твердых включений. Такие материалы должны иметь хорошие смазочные свойства, высокую теплопроводность, стабильные состав и структуру при температуре эксплуатации. Они должны быть химически инертны по отношению к конструкционным материалам, нетоксичны, термодинамически несовместимы с герметизируемой средой.
В двойных сальниковых уплотнениях с разрежением перед уплотнением в качестве разделительной среды чаще всего применяют техническую воду. При герметизации аммиака и сжиженных углеводородов с помощью двойных торцовых уплотнений в полость между последними закачивают масла, а также одно- и многоатомные спирты.
Твердые герметизирующие материалы – обширная совокупность веществ от пластичных композиций, приближающихся по свойствам к жидкости, до самых твердых и прочных конструкционных материалов.
Сальниковые набивки состоят из волокнистой основы, которая может быть пропитана жидкостью, содержать арматуру и наполнители. Различают волокнистые и комбинированные набивки. Волокнистые набивки подразделяют на хлопчатобумажные, лубяные (лен, конопля, джут), асбестовые, стеклянные, фторопластовые, капроновые, углеродные, металлические (медь, латунь, свинец и др.). Универсальное применение получили стойкие к износу и воздействию коррозионных сред набивки из фторопластовых или углеродных нитей.
Пропитка придает волокнистой основе формоустойчивость, износостойкость и непроницаемость. В качестве пропитывающих компонентов используют нефтяные масла, технический вазелин, твердые углеводороды, жиры растительного и животного происхождения, резиновые смеси и клеи, синтетические смолы и полимерные материалы, например, суспензию фторопласта-4. Чтобы повысить износостойкость и прирабатываемость уплотнений, непропитанные, набивки модифицируют порошковыми материалами (графитом, дисульфидом молибдена, тальком и т.д.).
По способу изготовления различают набивки из чесаного волокна, крученые, плетеные, скатанные, формованные, прессованные. Крученые набивки получают путем кручения нитей. Методом многократного плетения волокон (мультифлекс) в поперечном сечении набивки создают плотный каркас, обеспечивающий износостойкость и эластичность герметизирующего материала. Скатанные набивки изготавливают скатыванием полосы прорезиненного материала в тугой шнур. Графитовые ленты формуют из волокон графита и суспензии фторопласта-4. Комбинированные набивки состоят из нескольких волокнистых материалов или содержат в волокнистой основе армирующие элементы. При их плетении комбинируют органические и неорганические волокна, например, фторопластовые и углеродные, а также проволоку из цветных металлов и сплавов. Известны технологии, включающие оплетку волокнами резиновых шнуров и пластмассовых трубок, скатывание полосы ткани на сердечниках. Набивки, эксплуатируемые при высоких давлениях и температурах, изготавливают в виде колец из прессованной фольги – алюминиевой, медной, свинцовой и др.
Порошковые материалы для уплотнений нового типа, предохраняющих узлы трения от абразивных сред, представляют собой порошки ферромагнитных металлов (никель, железо) дисперсностью 10 – 50 мкм и их смеси с твердыми смазками (графит, дисульфид молибдена) с соотношением компонентов около 3:1.
Резина – эластичный материал, образующийся в результате вулканизации каучука. В промышленных условиях ее получают путем переработки так называемой резиновой смеси, содержащей, кроме каучука и вулканизующих агентов, наполнители, пластификаторы, стабилизаторы и другие компоненты. Достоинства резины, оптимально отвечающие назначению герметизирующего материала, выделяют ее из совокупности машиностроительных материалов.
Резина в широком интервале температур сохраняет уникальное свойство каучуков – высокую эластичность, т.е. способность к большим обратимым деформациям, а также стойкость в средах и непроницаемость. С позиций герметологии резина является однородным и изотропным материалом: показатели ее свойств постоянны в объеме герметизатора и одинаковы во всех направлениях. Резина практически несжимаема. Наблюдаемое при больших деформациях (l> 400%) уменьшение объема вызвано изменением ее физического состояния вследствие кристаллизации.
Благодаря сшивке каучуков в процессе вулканизации резина приобретает хорошие механические свойства. При многократном повторении цикла «нагружение-разгрузка» в медленном режиме, когда силы инерции близки к нулю, деформации новой резиной детали почти совпадают, отличаясь только для первых (тренировочных) циклов. Релаксационная природа упругости резин проявляется в постепенном уменьшении напряжения в медленно деформируемом материале. Это приводит к снижению герметизирующего давления в контактных уплотнениях с течением времени. Под действием постоянной нагрузки резина подвержена ползучести. Накопление остаточной деформации при контактировании со средами связана с набуханием резины либо с вымыванием ее компонентов. Резина отличается высокой износостойкостью в узлах трения на водяной смазке.
В уплотнениях широко применяют губчатую резину, которую изготавливают из твердых каучуков с помощью порообразователей, а также механическим вспениванием латексной смеси. Высокая герметизирующая способность при небольших контактных давлениях характерна для губчатой резины с замкнутыми порами. Африкционную резину получают путем радиационной прививки к ней пленок фторопласта. Такой герметизирующий материал соединяет достоинства резины и высокие триботехнические характеристики, свойственные фторопластам. Область его применения распространяется от вакуума до химически активных сред. Герметизаторы из магнитотвердых резин могут обеспечивать плотный контакт с ферромагнитными деталями уплотнений, заполняя неровности сопрягаемых поверхностей или принимая их форму, даже при отсутствии внешнего контактного давления. Они находят применение в конструкциях, сочетающих особенности контактных и магнитожидкостных уплотнений.
Конструкционные полимеры в отличие от резины находятся при эксплуатации не в высокоэластическом, а в стеклообразном или кристаллическом состоянии. По деформационно-прочностным характеристикам и степени проявления вязкоупругости они по сравнению с резинами ближе к твердому телу, чем к жидкости. Их достоинствами являются высокое химическое сопротивление и технологичность при переработке в герметизаторы. Специфическое свойство полимеров – самосмазывание, т.е. способность образовывать в зоне трения с металлическим контртелом противозадирные смазочные слои. В номенклатуру герметизирующих материалов входят следующие конструкционные термопласты: полиолефины, поливинилхлорид, фторопласты, полиарилаты, полиамиды, полиимиды, кремнийорганические полимеры, полиуретаны и др., а также композиты на их основе.
Металлические прокладочные материалы – алюминий марок А0, АД1, АД0; латунь Л62; никель НП1, НВК; свинец С2; медь Ml, M2, МЗ; сталь низкоуглеродистая 05кп, 05 и 08, а также Ст2 и СтЗ; сталь коррозионностойкая 12Х18Н10Т, 08Х18Н10Т.
Комбинированные прокладки содержат металлические и неметаллические компоненты. Армированное асбестовое полотно представляет собой прорезиненную ткань из нитей, полученных скручиванием латунной проволоки и асбестовой ровницы. Спирально навитые прокладки формируют путем свертывания в кольцо металлической ленты фасонного профиля и паронита или асбестовой бумаги. Кассетные прокладки содержат вязкоупругий неметаллический сердечник, заключенный в кассету из металла.
Углеродные материалы – совокупность композиционных материалов триботехнического назначения, содержащих компоненты на основе углерода. Материалы на углеродной и графитизированной матрицах изготавливают прессованием кокса, сажи или графита на связке из пека, с последующим обжигом и термообработкой при 2400 – 2600 ºС. Углеродные матрицы прочнее графитизированных, но менее теплопроводны. В матрицах обеих типов имеются поры диаметром 1 – 5 мкм, составляющие около 12 – 20 %. Матрицы пропитывают полимерными составами расплавами металлов, растворами солей. Силицированные графиты – материалы на графитовой матрице, подвергнутой силицированию, т.е. пропитке кремнием при температуре свыше 2000 °С. В результате образуются жесткий каркас из карбида кремния и сетка графита, придающая материалу высокие теплопроводность и триботехнические характеристики. Общим недостатком материалов на углеродной и графитовой матрицах является низкая ударная вязкость и хрупкость.
К углеродным материалам относят углеродопласты – пластмассы, содержащие волокна в виде жгутов, матов, в виде рубленых волокон. Эти прочные химически и термически стойкие материалы нашли применение в подвижных уплотнениях. Для герметизации агрессивных сред используют графитофторопластовые материалы, менее прочные по сравнению с углеродными, но практически непроницаемые для жидкостей.
Металлы как конструкционные герметизирующие материалы, применяет преимущественно в торцовых уплотнениях. Герметизаторы из закаленной хромистой стали успешно работают в паре с углеродными материалами. При недостаточной смазке используют хромистые чугуны, легированные никелем, хромом или медью для повышения коррозионной стойкости. В парах с углеродными материалами, пропитанными металлом, успешно работает свинцовистая бронза. В уплотнениях клапанов используются медь, алюминий, а в ответственных узлах – серебро и другие драгоценные металлы.
Поршневые кольца для герметизации цилиндров гидравлических систем, компрессоров и двигателей внутреннего сгорания изготавливают преимущественно из антифрикционного чугуна. Для повышения прирабатываемости и износостойкости на кольцах формируют покрытия из цветных металлов (медь, хром, олово, свинец, индий) или твердых сплавов. Иногда их изготавливают из марганцовистых сталей и бронзы.
Специфическим герметизирующим материалом на основе металлов является материал металлорезина (МР). Его получают из проволоки (бронза, марганцовистая или хромоникелевая сталь и др.) диаметром 0,1 – 0,15 мм путем навивки спиралей с диаметром навивки 1,5 – 2,0 мм и шагом, равным диаметру навивки, с последующим прессованием определенным образом уложенных спиралей до плотности 1,5 – 2,0 г/см3. Такой материал по упругости формы и деформационно-прочностным характеристикам при сжатии является аналогом резины. Его используют в контактных уплотнениях в сочетании с полимерными материалами, выполняющими функции непроницаемого барьера и скользящего элемента.
Металлические сильфоны выполняют преимущественно из хромоникелевых коррозионностойких сталей аустенитного класса (12Х18Н10Т, 08Х18Н10, 04Х18Н10 и др.). Широкая номенклатура металлов и сплавов используется для изготовления предохранительных мембран (ряд составлен в порядке увеличения минимального разрывного давления): свинец, алюминий, серебро, платина, палладий, медь, монель-металл, никель, золото, инконель, нержавеющая сталь, титан, углеродистая сталь.
Твердые сплавы – композиционные материалы на основе карбидов металлов и пластичного металла – связки (кобальт, никель и др.). Высокую прочность и износостойкость они сохраняют при нагревании до 1000 °С. Их можно применять в подвижных уплотнениях, эксплуатируемых при недостаточном смазывании и перепадах температуры. Основная область применения твердосплавных герметизаторов на кобальтовой связке – абразивосодержащие среды. Из-за низкой химической стойкости кобальта их нецелесообразно использовать в оборудовании химической промышленности, а поскольку кобальт является радиоактивным изотопом, – и в уплотнениях насосов атомных электростанций.
Керамика – совокупность композиционных материалов, получаемых спеканием размельченных горных пород, минералов, окислов и других неорганических составляющих. Исключительность керамики как герметизирующего материала обусловлена ее химической стойкостью в средах с сильными окислительными свойствами, в которых другие материалы не работают, например в олеуме.
Наиболее распространенная в технике группа керамических материалов – оксидная керамика. Ее компонентами являются дешевые и недефицитные оксиды алюминия, циркония, магния, лития, бериллия и ряда других металлов. Из оксидной керамики изготавливают герметизаторы торцовых уплотнений, диски и импеллеры для динамических уплотнений, детали затворов пробковых кранов и т.д. Керамику на основе оксидов бериллия, тория и урана применяют в конструкциях герметичных циркуляционных контуров, используемых в атомно-энергетическом машиностроении. Вторая большая группа керамических материалов – карбидная, нитридная и боридная керамики. Они обладают самой высокой среди конструкционных материалов твердостью, стойки к окислению при температурах свыше 1000 °С, износостойки. Их перерабатывают в герметизаторы методами порошковой металлургии. Основная область применения в уплотнительной технике – высокотемпературные уплотнения энергетической арматуры.
Использование керамики как герметизирующего материала долгое время сдерживалось из-за ее основного недостатка – хрупкости. Герметизаторы из керамики склонны к растрескиванию при резком охлаждении и нагреве. Поэтому режим недостаточного смазывания для подвижных пар керамика-керамика обусловливает быстрое разрушение керамических уплотнений. Керамические герметизаторы оптимально работают в парах трения с самосмазывающимися материалами. Наиболее эффективным способом устранения хрупкости керамики является повышение однородности и мелкозернистости ее структуры – устранение пор, агломератов частиц, химических примесей. Для этого используют тонкий размол исходного порошка, повышение температуры отжига изделий и др. Для переработки такой керамики можно использовать экструзию, волочение, ковку.